Beginner's guide to pocket hole joinery WOODWORKING BASICS
Big award show this weekend. I really hope Leo wins for his riveting performance as ... Love it or hate it, pocket hole joinery has made making things a lot easier for a whole new generation of builders.
There's a lot to like about the technique. You can build things that are very strong with no special skills or experience needed. And the cost of getting started is relatively affordable. My show is mostly project based. Usually I'm more interested in getting something made rather than the process of making.
I do like to find a balance between enjoying the process and having fun, yet not getting bogged down in complex skills. However, there are a lot of people whose focus is tilted more towards technique and fine craftmanship.
I admire those of you who will spend six months or more working on an amazing heirloom quality project with hand-cut dovetails and mortise and tenon joinery. Making things is fun and rewarding no matter how you approach it. This video is for people who are new to or inexperienced with woodworking but want to get started making and completing projects without a lot of fuss.
And maybe after completing a few quick and easy projects using pocket screws, you may gain the confidence to explore more complex joinery techniques. The possibilities are endless. One thing I want to mention is that all of my pocket hole tools are from Kreg. Kreg does not sponsor Woodworking for Mere Mortals, nor am I compensated for this video. There are other brands that make pocket hole jigs too, I'm just familiar with the Kreg jig.
Sometimes screwing into the end-grain of a board is fine but it isn't the strongest connection. Think of the end-grain of wood like this stack of pencils with all of the fibers running in this direction.
When you screw into them the wood fibers can just separate without giving the screw much to bite into. Screwing into the edge- or the face-grain of a board will give you much better holding power. So in a situation like this the problem is how to join the boards together this way so that the screws aren't going into the end-grain.
The solution is to drive a screw through this face-grain at an angle into that face-grain. To make a strong connection you need a special drill bit and a special screw. This is a stepped bit; it has a narrow tip for guiding the screw, and a wider part for making the pocket hole. This area where the two sections meet creates a flat ledge that the head of the special pocket screws rest on. I've cut away this board so you can see how the wide, flat head of the screw holds tight against that ledge.
It's kinda like a screw with a built-in washer.
It's a good idea to attach the jig to something so it doesn't move. First, you'll need to adjust this thing to match the thickness of the wood you're using. There's markings on the side and positive stops I've rarely had to adjust that because I almost always drill pocket holes in three-quarter inch thick boards. Next you need to set the depth of the hole by adjusting this collar on the drill bit.
You loosen it with a hex wrench. Then drop the bit into one of these guide holes. I let it touch the plastic base, then I back it off just a hair. Then I can lock down this collar. So that'll stop the bit from drilling into the base.
And this is also something I rarely need to adjust. Adjust this part to the thickness of your board. One other thing I highly recommend is this vacuum attachment. It's amazing how much of a mess drilling these holes makes. Hooking up a shop-vac removes almost all of it.
Using the pocket hole jig is simple. There are three guide holes that help you to space apart your pocket holes however you like. Then you just set your board in place and lock it down. With your drill set to its highest speed, drill into the board until the collar stops it. Usually you'll drill on the ends of the boards.
But sometimes, say if you want to join two boards together like that, you may need to drill along the edge. The important thing to remember is that the point of the screw needs to go into the edge-grain, or the face-grain, so a connection going this way would make for a weak joint. On the packages of the screws there's a chart to help you figure out what length of screw you'll need. Obviously you want the screw to go into the board as far as possible without poking through the other side. And running a couple of tests on some scrap boards is always a good idea.
Most of the time I use inch and a quarter screws since I most use three-quarter inch thick lumber.
Also the screws come in fine or coarse thread. I use the fine thread screws only for hard woods like oak or maple. For almost all other lumber and plywood use the coarse thread screws. Basically I just keep a supply of the inch and a quarter coarse thread screws on hand at all times.
To join the boards they need to be clamped together while driving the screws. If you don't, the twisting motion of the screw will shift them apart, and they won't be flush. For joining together flat edges like for a picture frame or the face frame of a cabinet I use this clamp right across the joint to keep the boards in place.
These are square drive screws, and one of these long drivers makes it easy to drive them. Set your drill to a slow speed.
I usually drive the screws in by feel, stopping just when I feel them tighten. Be careful you don't drive them too fast or with to much torque which can cause them to blast all the way through the wood. For that reason I also don't recommend using an impact driver. If you're afraid you might drive the screws in too deep, the safest technique is to adjust this clutch on your drill - you know, this thing that you probably never use and maybe you didn't even know what is was for.
Set it to a low number, then it'll tighten the screw but stop before it drives it in too far.
You'll probably be surprised how strong that joint is. Now let's say you wanna join your pieces together at a ninety degree angle, say for a bookcase or a box. You still need to clamp them together but obviously this kind of a clamp won't work. One method is to use a bar clamp or a pipe clamp. You can also use one of these specialty clamps that works like this.
Be aware of the direction your screws are going. Always make sure they're going into the meat of the wood so to speak. In other words, you always want the screws angled in toward the main part of the board, not toward the end. There's just not enough wood there to hold it. One of the drawbacks to using pocket holes is that they can be an eyesore.
Usually it's pretty easy to conceal them in the back or underneath projects in such a way that they're not visible.
But sometimes on projects it's just impossible to avoid placing them in a visible location. The easiest way to hide them is to plug the holes. You can either buy these pre-made wooden plugs or you can just use a dowel, glued into place and sanded flush. For painted projects especially, that's a good solution.
Once it's painted over you'll never see that patch. So let me know what you think about pocket hole joinery. Do you use pocket srews, and if so do you have any tips and tricks you'd like to share with others? Please leave your comments and questions about pocket holes down below and I'll answer some of those early next week on More Minutes. Thank you for joining me for another basics video.
Have a great week, and I'll see you next Friday..
https://www.trafficwave.net/cgi-bin/newmember/enrlform.cgi/yosehbaez/paid
Thanks for your visit!
https://youtu.be/mvO6zaIUO18
https://bit.ly/3MSmyyD
Subscribe to:
Post Comments (Atom)
YT Explosion Code Review" Week 1 Results
Hi guys Kelita and I wanted to come and give you a YouTube explosion code review and this review is really from my first week of being invol...
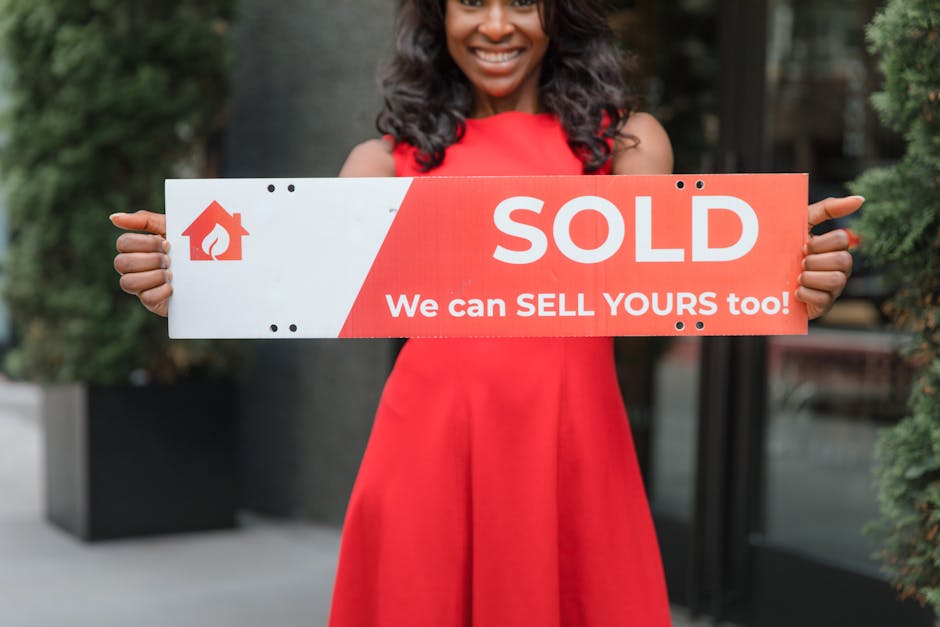
-
Do you want a relatively easy way to make money? If so, you should consider attending and participating in mini storage auctions. These au...
-
Best Way To Generate More Leads Online & Lead Magnet Ideas for Network Marketing Hey guys, it's Trey Bearor from TreyBearor.com H...
-
Hi guys Kelita and I wanted to come and give you a YouTube explosion code review and this review is really from my first week of being invol...
No comments:
Post a Comment